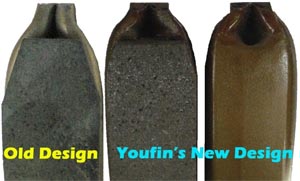
Youfin's constant benchmarking and R&D effort has successfully developed an innovative shoe manufacturing Process that eliminate its current short coming
The new shoe geometry includes a larger and un-disrupted surface at the tip of the shoe Platform This enhanced topography not only enables an increase in lining area locally, it also improves structural support to the lining allowing maximum performance and durability potential of the shoe to be achieved
In addition, contrary to the original 'expand-and-grind' method, a non expanded, cam profile controlled or numerical cont rolled lining grinding technique has beendeveloped by Youfin to complement the shoe platform upgrade.
This is consistent with Youfin s adopted philosophy of continuous improvement and continuous innovation.
This feature is currently protected by a provisional patent application.
|